Difference between revisions of "42Q-MES0186-A-PTS Mobile"
Line 6: | Line 6: | ||
| | ||
<center>'''Production'''</center> <center>'''100% Traceability'''</center> <center>'''PTS Mobile'''</center> <center>''' MES 15.78'''</center> | <center>'''Production'''</center> <center>'''100% Traceability'''</center> <center>'''PTS Mobile'''</center> <center>''' MES 15.78'''</center> | ||
− | |||
<span class="mw-headline" id=""> </span> | <span class="mw-headline" id=""> </span> | ||
<span class="mw-headline" id=""> </span> | <span class="mw-headline" id=""> </span> | ||
+ | | ||
− | + | = <span class="mw-headline" id="Introduction"><span class="mw-headline" id="Introduction"><span class="mw-headline" id="Introduction"><span class="mw-headline" id="Introduction">Introduction</span></span></span></span> = | |
− | = <span class="mw-headline" id="Introduction"><span class="mw-headline" id="Introduction"><span class="mw-headline" id="Introduction">Introduction</span></span></span> = | ||
The Part Traceability System (PTS) is an essential component of the MES suite of tools, designed specifically to meet the growing demands of customers. Its primary objective includes offering comprehensive traceability at the component level and ensuring strict quality controls. By automating production lines and enforcing rigorous product quality control, this system plays a pivotal role in enhancing overall productivity. its successful implementation has been witnessed across numerous plants worldwide. As technology continues to evolve and SMT process equipment tools become increasingly intricate and feature-rich, the PTS application and its accompanying features consistently advance. However, our commitment remains to provide support for all technology tools. 42Q prioritizes offering the necessary flexibility to accommodate various line types and deliver diverse levels of traceability that are crucial to the success of your business. | The Part Traceability System (PTS) is an essential component of the MES suite of tools, designed specifically to meet the growing demands of customers. Its primary objective includes offering comprehensive traceability at the component level and ensuring strict quality controls. By automating production lines and enforcing rigorous product quality control, this system plays a pivotal role in enhancing overall productivity. its successful implementation has been witnessed across numerous plants worldwide. As technology continues to evolve and SMT process equipment tools become increasingly intricate and feature-rich, the PTS application and its accompanying features consistently advance. However, our commitment remains to provide support for all technology tools. 42Q prioritizes offering the necessary flexibility to accommodate various line types and deliver diverse levels of traceability that are crucial to the success of your business. | ||
Line 19: | Line 18: | ||
| | ||
− | = <span class="mw-headline" id="PTS_Mobile"><span class="mw-headline" id="PTS_Mobile">PTS Mobile</span></span> = | + | = <span class="mw-headline" id="PTS_Mobile"><span class="mw-headline" id="PTS_Mobile"><span class="mw-headline" id="PTS_Mobile">PTS Mobile</span></span></span> = |
PTS Mobile is specifically designed to be compatible with handheld devices, recognizing that operators may not always be in front of a computer and require the convenience of using a handheld device for operation. | PTS Mobile is specifically designed to be compatible with handheld devices, recognizing that operators may not always be in front of a computer and require the convenience of using a handheld device for operation. | ||
Line 27: | Line 26: | ||
To access PTS Mobile, navigate to '''Production > 100% Traceability > PTS Mobile'''<br/> <br/> | To access PTS Mobile, navigate to '''Production > 100% Traceability > PTS Mobile'''<br/> <br/> | ||
+ | | ||
− | + | == <span class="mw-headline" id="Re-Validate_Material"><span class="mw-headline" id="Re-Validate_Material"><span class="mw-headline" id="Re-Validate_Material"><span class="mw-headline" id="Re-Validate_Material"><span class="mw-headline" id="Re-Validate_Material"><span class="mw-headline" id="Re-Validate_Material">Re-Validate Material</span></span></span></span></span></span> == | |
− | == <span class="mw-headline" id="Re-Validate_Material"><span class="mw-headline" id="Re-Validate_Material"><span class="mw-headline" id="Re-Validate_Material"><span class="mw-headline" id="Re-Validate_Material"><span class="mw-headline" id="Re-Validate_Material">Re-Validate Material</span></span></span></span></span> == | ||
Whenever material is going to exhaust, splicing is required to ensure production can proceed without interruption. However, there is a small chance that splicing was mistakenly done to the wrong feeder slot and it can’t be detected by the normal part verification process. | Whenever material is going to exhaust, splicing is required to ensure production can proceed without interruption. However, there is a small chance that splicing was mistakenly done to the wrong feeder slot and it can’t be detected by the normal part verification process. | ||
Line 39: | Line 38: | ||
'''Figure 1: Re-Validate Material''' | '''Figure 1: Re-Validate Material''' | ||
− | [[File:PTSM RevalidateMaterial.png|900px]] | + | [[File:PTSM RevalidateMaterial.png|900px|PTSM RevalidateMaterial.png]] |
| | ||
Line 45: | Line 44: | ||
The main screen will request the user to input or scan the Workstation, Material Barcode, Feeder Barcode, and Station Location. | The main screen will request the user to input or scan the Workstation, Material Barcode, Feeder Barcode, and Station Location. | ||
+ | | ||
− | == <span class="mw-headline" id="Load.2F_Unload_Materials"><span class="mw-headline" id="Load.2F_Unload_Materials">Load/ Unload Materials </span></span> == | + | == <span class="mw-headline" id="Load.2F_Unload_Materials"><span class="mw-headline" id="Load.2F_Unload_Materials"><span class="mw-headline" id="Load.2F_Unload_Materials">Load/ Unload Materials </span></span></span> == |
It is mainly used for material loading and unloading, including the following submenus: | It is mainly used for material loading and unloading, including the following submenus: | ||
Line 60: | Line 60: | ||
<br/> <br/> '''Figure 2: Load / Unload Materials page''' | <br/> <br/> '''Figure 2: Load / Unload Materials page''' | ||
− | '''[[File:PTSM Load UnloadMaterials page.png|900px]]''' | + | '''[[File:PTSM Load UnloadMaterials page.png|900px|PTSM Load UnloadMaterials page.png]]''' |
+ | |||
+ | | ||
+ | |||
+ | | ||
+ | |||
+ | # | ||
+ | === '''Load Material [[File:PTSM Logo1.png]]''' === | ||
+ | |||
+ | <br/> | ||
+ | '''This function is to prepare for the Scan board.''' | ||
+ | | ||
+ | '''Figure 3: Load to Workstation ''' |
Revision as of 15:26, 7 August 2023
42Q Home >Production > 100% Traceability> PTS Mobile
Contents
Introduction
The Part Traceability System (PTS) is an essential component of the MES suite of tools, designed specifically to meet the growing demands of customers. Its primary objective includes offering comprehensive traceability at the component level and ensuring strict quality controls. By automating production lines and enforcing rigorous product quality control, this system plays a pivotal role in enhancing overall productivity. its successful implementation has been witnessed across numerous plants worldwide. As technology continues to evolve and SMT process equipment tools become increasingly intricate and feature-rich, the PTS application and its accompanying features consistently advance. However, our commitment remains to provide support for all technology tools. 42Q prioritizes offering the necessary flexibility to accommodate various line types and deliver diverse levels of traceability that are crucial to the success of your business.
PTS Mobile
PTS Mobile is specifically designed to be compatible with handheld devices, recognizing that operators may not always be in front of a computer and require the convenience of using a handheld device for operation.
To access PTS Mobile, navigate to Production > 100% Traceability > PTS Mobile
Re-Validate Material
Whenever material is going to exhaust, splicing is required to ensure production can proceed without interruption. However, there is a small chance that splicing was mistakenly done to the wrong feeder slot and it can’t be detected by the normal part verification process.
Therefore, a material re-validation is required to handle this scenario. By re-validate material (just re-scan material barcode, without interrupting the current production run), chances of splicing material to the wrong feeder slot can be avoided. The Re-Validate Material is a mobile solution (GUI) to handle the situation of Component Reset and Re-validation for traditional SMT Machines. The users can validate the materials with the Workstation, Material Barcode, Feeder Barcode, and Station.
Figure 1: Re-Validate Material
The main screen will request the user to input or scan the Workstation, Material Barcode, Feeder Barcode, and Station Location.
Load/ Unload Materials
It is mainly used for material loading and unloading, including the following submenus:
- Load Material
- Load SMT Tools
- Material Queue
- Scan Barcode
- Prepare Material
- Unload Material
- Load Prepare Material
Figure 2: Load / Unload Materials page
PTSM Load UnloadMaterials page.png
Load Material 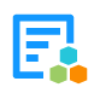
This function is to prepare for the Scan board.
Figure 3: Load to Workstation